Blog
View All Blog Postings
Ethical Standards of Professional Engineers
In matters dealing with public and safety, it is important to maintain a high level of trust in officials responsible for dealing with these matters. Professional Engineers are held to the same high ethical standards. The National Society of Professional Engineers states in their Code of Ethics for Engineers that “Engineers, in fulfillment of their professional duties, shall:
- Hold paramount the safety, health, and welfare of the public.
- Perform services only in areas of their competence.
- Issue public statements only in an objective and truthful manner.
- Act for each employer or client as faithful agents or trustees.
- Avoid deceptive acts.
- Conduct themselves honorably, responsibly, ethically, and lawfully so as to enhance the honor, reputation, and usefulness of the profession.”
Of course, traits such as honesty and trustfulness are to be expected of professional individual, but due to the risks associated with poor engineering, Professional Engineers must be held to a higher level of accountability. For example, an engineer specializing in wood-framed residential construction should not be stamping design documents for a hydroelectric dam! Additionally, Professional Engineers must also dedicate a portion of their professional development hours to ethics training or risk losing their license entirely. Overall, these high ethical standards ensure that a Professional Engineer will design, build, and maintain structures that can safely service the public for years to come.
Structural Issues Due To Leaking HVAC Units
Leaking interior HVAC units can cause massive headaches for property owners, but they can also cause significant structural damage if they are not repaired promptly. Interior HVAC units can leak for numerous reasons, including clogged or disconnected condensation drain lines, poorly maintained filters, and low refrigerant levels causing condensate lines to freeze and thaw. While disregarding a leaking HVAC unit could lead to further issues with the unit, it could also cause damage to structural elements supporting the floor and HVAC unit as well. Both wood and concrete structural slab systems are susceptible to long term moisture exposure, and as the moisture exposure continues for prolonged periods of time, the damage caused by this leaking water could grow exponentially.
In some cases, HVAC units maybe located on the floor above a crawlspace causing the structural damages caused by these leaks to go unnoticed until intensive investigations are performed. The accompanying picture shows heavily deteriorated wood subfloor and floor joists below an HVAC unit that had been leaking for a prolonged period of time. A larger area of the subfloor had to be complete replaced, and the joist themselves had to be strengthened with supplemental joists to ensure that the floor was structurally stable. Placement of a drainage pan with a “wet switch” can help catch a leak right as its starting, and regular cleaning of the drain lines helps prevent clogs caused by debris and dirt. Repairing a leaking HVAC may not only ensure that your building stays cool during the hot summer months, but also prevents costly, invasive repairs.
Removing Snow From Parking Structures
Proper removal of snow from a parking garage is usually the first thing on the owner’s mind after a snowstorm to the allow the garage’s top deck to become operational again. However, some owners may not realize that improper removal of the snow could jeopardize their structure, particularly if all the snow is stored on a single location on the top deck. Most buildings within the surrounding area are designed to withstand a code-prescribed snow load of approximately 30 pounds per square foot (psf). However, stacking large amounts of wet, melting snow in a concentrated area can cause loads double or triple the design load to be applied to the structure, risking its structural integrity and, in the worst case scenarios, leading to failure.
There are several more building-friendly ways to remove this snow and get the parking open again. One way to remove the snow would be close the top deck to vehicular traffic until the snow melts; however, given the amount of snow and conditions following the storm, this could take several days. De-icing salts could be used to accelerate the melting of the snow, but if the slab has never received a protective coating, the chloride-heavy melted snow could penetrate into the slab and accelerate deterioration of the steel reinforcement within the slab. If the owner chooses to remove snow off of the top deck through use of shovels and plows, special equipment may need to be used to ensure any coatings on top of the slab are not damaged. Ultimately, the best way to remove snow following a storm depends on the needs and composition of your specific structure.
“Check” This Out!
The new wood deck repairs throughout your community have been coming along nicely, and the repairs make the decks themselves look almost brand new. However, a few weeks after repairs are finished, you make a startling discovery: the new wood members are beginning to crack! Were the repairs completed improperly? Was subpar wood used? Have you wasted time and money on repairs that will need to be redone? Fortunately, most of the cracks you are seeing in the new wood members are a natural part of the wood’s acclimation process. As “green” (i.e. wet) wood naturally dries over time, it shrinks, causing cracks to form along portions of the wood. A “check” is a crack that occur parallel to the grain of the wood, while a “shake” is a separation of the growth rings within the lumber. While these cracks may appear unsightly, they usually do not affect the structural properties of the wood, unless the check or shake runs through the entire depth of the wood member. Properly acclimating the wood pieces to environmental conditions and specifying higher grade lumber can help minimize this cracking, but green lumber will always display some external cracks as it dries. Also, additional cracks may occur as the wood is exposed to varying environmental conditions throughout the seasons. If you still have concerns about cracks in your wood structures, ETC can help evaluate these cracks and put your mind at ease
Strong Roots, Weak Foundations
Usually when thinking about planting a new tree, landscape aesthetics and shading plays a very big part in the decision-making process. However, proximity to your structure should be a consideration as well. While a tree may appear to be a reasonable distance away from you structure, tree roots can spread as far as five time the radius of the tree canopy and can grow underneath foundations and, in extreme cases, through cracks in your foundation walls. These roots can swell and contract during heavy rains and prolonged droughts, respectively, disrupting the soils below the foundation and leading to potential settlement of the foundation. Roots of trees too close to retaining walls can place intense pressure along the rear of these structures, causing bulges to form or even causing the wall to fail completely, as seen in the adjacent photograph. Foundation and retaining wall issues can be extremely costly to repair and greatly impact the lives of residents in your structure, as opposed to removing improperly placed landscaping before they cause structural issues. If you have any concerns regarding landscaping impacting your structure, ETC can help you examine your options before they become a problem!
The Power of Small Liquid Droplets
It has long been known that water has the ability to erode some of the hardest materials on earth given enough time but the mechanics of how this occurs has only recently been studied. At the University of Minnesota Twin Cities, researchers have discovered why small liquid droplets cause the erosion of solid surfaces. Using a new analysis technique called high-speed stress microscopy that measures the force and pressure exerted on a surface as a drop contact it, the researchers have discovered that the force of a droplet spreads out as the drop deforms itself on impact. This deformation happens faster than the speed of sound, unleashing a shockwave along the surface of the solid object: “Each droplet behaves like a small bomb, releasing its impact energy explosively and giving it the force necessary to erode surfaces over time”. This discovery is expected to help material developers and engineers create better erosion-resistant coatings and materials that weather the elements better than current systems.
University of Minnesota. “New study solves mystery of how soft liquid droplets erode hard surfaces.” ScienceDaily. ScienceDaily, 31 March 2022.
Maintenance of Metal Guardrails
Metal guardrails can provide stylish, long-term fall protection for balconies, walkways, garages, and many other elevated structures. While metal guardrails can last almost twice as long as wood guardrails, periodic maintenance is still required to ensure they remain serviceable and do not pose any life-safety hazards due to deterioration of the aging railing components. A few steps taken every few years can allow these vital building components to last well into the future of the building:
- Understand your railings. Are they aluminum or steel? Do they have a protective coating such as a powder coating? Are they surface mounted or embedded into a concrete slab? The answer to these questions and many more are crucial to determining exactly which approach is best for maintaining your railings!
- Routine cleaning of the guardrails will help remove built-up organic growth and other stains that could contribute to deterioration of the railing finishes.
- Make sure water has a way to get out of the railings. Many times, these railing systems are comprised of numerous hollow tubes which can trap water that enters the railings through cracks or holes or from condensation build up. The placement of weep holes throughout the assembly and especially at the post bases can help evacuate water from the railing interior, reducing the potential for corrosion of the metal.
- Restore protective coatings. Peeled/missing coating will expose the underlying metal member to elements, exacerbating corrosion at these areas. Recoating railings will ensure this protective cover between the metal and the environment will remain effective.
- Clean corrosion as soon as possible! It is imperative to clean corrosion from steel members before it progresses to section loss. If holes start appearing in the guardrails due to corrosion, more intensive repairs measure will be required, including replacement of the member.
If you are looking for a professional evaluation of your building’s railings, ETC can provide the evaluation services you need.
Types of Wood Members
As construction techniques continue to grow and evolve, choosing the right material for your job may seem a little overwhelming. This especially rings true with timber construction. Gone are the days when you just needed to specify the size and tree species. Here’s a guide to help you choose the timber that is best suited for your job.
Sawn Wood‐ Traditional sawn wood is still the commonly used type of lumber. Almost all structural sawn wood beams originate from softwood tree species, such as Pine or Douglas Fir. Structural sawn lumber is further classified through stress‐gradings, which establish standard working values for properties that can be used to determine the load‐bearing capacity of these members. Typical lumber grades can be seen on the adjacent table. Traditional sawn lumber can be used for almost all structural member, such as joists, beams, posts, etc.
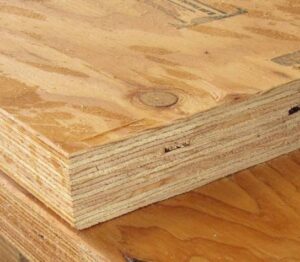
Laminated Veneer Lumber (LVL)‐ Laminated veneer lumber belongs to a family of engineered wood products called structural composite lumber (SCL). Structural composite lumber members are comprised of blocks of lumber materials know as “billets”, which are veneers, strands or flakes of dried and graded woods adhered together. For LVL beams, thin wood veneers are bonded together into a billet, with the grain of all veneers running parallel to the length of the beam. Called “parallel lamination”, this orientation allows LVL beams to exceed the load‐bearing bearing capacity of similarly sized sawn lumber and be used for long‐spanning load‐bearing members, such as beams or rafters.
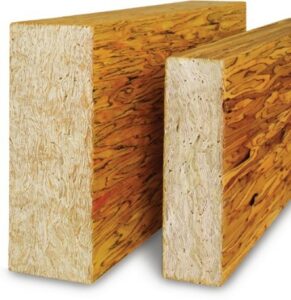
Parallel Strand Lumber (PSL)‐ Parallel strand lumber, another type of structural composite lumber, is manufactured using long, thin strands of wood (typically the waste material from plywood manufacturing), which are laid parallel and bonded together to form a billet. Similar to LVL members, PSL members can be used for long‐spanning beams where greater load‐bearing capacity is required. Additionally, PSL members are also frequently used as columns.
Laminated Strand Lumber (LSL)‐ Similar to PSL, laminated strand lumber is comprised of long, flaked wood strands of hardwoods not normally used for structural applications (e.g. maple). The wood strands used for LSL are typically shorter and thicker then those used in PSL, leading to lower load‐bearing capacity. Typically, LSL members are used for wall framing, such as studs and headers. LSL members can also be used for intermediate spanning beams and rim boards, where the higher strength LVL or PSL members are unnecessary.
Oriented Strand Lumber (OSL)‐ Oriented strand lumber is comprised of flaked wood strands strands very similar to those used in LSL member, but the length of the strand has been reduced and the thickness increased. As such, OSL members can typically be used in similar situations where LSL members are utilized
What to Look for When Concrete Deteriorates
As with all building components, concrete slabs, beams, and columns will inevitably deteriorate and need repair throughout the lifetime of a building. Most concrete deterioration is linked to the corrosion of embedded metal elements, such as steel reinforcement bars. As the steel elements rust, it expands and occupies more space than the original steel, slowly building up pressure on the concrete until the concrete separates from the steel reinforcement. In the most extreme cases, the concrete will separate from both the steel and surrounding concrete, resulting in a condition known as “spalling.” Spalled concrete can be easily identified by visual inspection; it would be hard to miss a chunk of concrete missing in a wall or beam!
However, deteriorated concrete that separates from the steel rebar, but not the surrounding concrete, can be trickier to find. This deterioration is known as “delamination.” Identifying delaminated concrete requires non-destructive testing, such as sounding of the concrete elements, which tends to be the most common cost-effective option. Areas of delaminated concrete can be found by listening for hollow areas, which make a low, drum-like noise, while sounding the concrete with a hammer or by chain dragging. The hollow sound is caused by the air gap between the separated concrete and rusted steel. If you’ve noticed some suspicious-looking concrete in your building, reach out to ETC to help evaluate your building today.
Benefits and Short-Comings of Glue-laminated Timber (Glulam)
Glue-laminated lumber (also known as Glulam) is a versatile and innovative material widely used in the construction industry and has become increasingly more popular in recent years for its many benefits. Glulam is composed of wood laminations that are bonded together with high-strength adhesives to form a strong member.
Benefits
Glulam members are customizable to be formed to specific lengths and curvature to fit the needs of most residential and commercial wood-framed properties. Most notably, in 2019, the construction of an 18-story building in Norway was formed from solely glulam and laminated timber beams. Glulam beams also have a much better environmental impact compared to steel or concrete beams for their carbon storage capacity. Furthermore, glulam beams have good fire resistance and can outlast steel beams due to a charred carbon layer that is formed on the surface of the beams which insulates against heat. In our industry, they are typically utilized to span large openings that regular timber beams cannot, like balcony door and breezeway openings.
Shortcomings
While the benefits for glulam beams look to be impressive, the necessity of glulam beams over other engineered lumber beams may not be the most cost-effective solution, as the cost for glulam beams are higher than they are for many other engineered lumber. Deterioration of glulam beams is common due to high humidity areas and water intrusion through improper or unsealed flashings. While glulam beams are often marketed for their ability to be exposed to the natural environment, they are often very susceptible to deterioration due to construction methodologies. Glulam beams are prefabricated to an exact size; therefore, if the beams need to be cut to fit new dimensions, the entire beam can become susceptible to deterioration if the cut portions are not properly protected with a sealer material on-site.
Planning a Wheelchair Ramp
We are excited to share our recently completed wheelchair ramp for a historic building in Washington DC. The building residents wanted a ramp that provides handicap accessibility for their residents. We designed the new ramp at the exterior of the building that slopes from the grade level to the basement level with interior elevators. The residents with a wheelchair now have handicap accessibility to all the levels of the building.
The process and construction required preparation of drawings and approvals from the Historic Preservation Office, Building Department and careful planning with Owners, Contractors and Manufacturers.
If you are planning to build a wheelchair ramp, also known as handicap accessible ramp (in a historic or non-historic building), it would be best to have a check list of design considerations before starting your project.
- Familiarize yourself with the International Building Code (IBC), American Disability Act (ADA) and American National Standards Institute (ANSI) A117.1 that determines rules and regulations for wheelchair ramps.
- Most of the states and local jurisdictions have adopted IBC governed by International Code Council. Always make sure to check with your local permit office for building code and permit requirements.
- Handicap ramp requirement is eight (8) percent slope, that means your ramp should not be steeper than one-unit vertical in twelve-units horizontal. For example, if you are planning a ramp for a height difference of twenty-four inches (2 feet vertical), it will require two-hundred and eighty-eight inches (24 feet horizontal) of floor space. Maximum vertical height allowed in any ramp is thirty (30) inches.
- Minimum ramp clear width is thirty-six (36”) inches, minimum headroom height is eighty (80”) and minimum landing width is sixty (60”) inches.
- The height of railings is between thirty-four (34”) and thirty-eight (38”) inches above walking surface. Handrail material can be wood or metal. We recommend finished wood handrail for interior ramps and corrosion-resistant metal handrail for exterior ramps.
- If the ramp is located at the exterior, plan for storm water drainage and connection to site drainage system.
- Safety comes first, consider slip-resistant finish material for the walking surfaces.
Cooling Season – Things To Consider
With the winter season and cold weather at a close, we turn our attention to the warmer spring months and the cooling of our buildings. This change of seasons can bring about new challenges for a building and owners may be concerned if their Heating, Ventilation, and Air Conditioning (HVAC) system is providing a safe environment and staying cost-effective. Although these are concerns throughout the year, you may be wondering how the warmer weather will impact your building and if it is time to evaluate your current HVAC system. There are many “Things to Consider” when it comes to warmer weather and once you understand what is affecting your building, you can approach solutions to make them better. Read on to learn about some strategies you can invest in to make your building healthier and more cost-effective during the spring.
At this time of year, plants begin to bloom and there tends to be large quantities of pollen in the air, which can reduce the overall outside air quality. This air can make its way to your mechanical equipment, and eventually to the inside of your building, which may adversely affect occupants. To combat this issue, it is highly recommended to change air handling unit filters more frequently and possibly consider filters with a higher Minimum Efficiency Reporting Value (MERV) rating. This rating specifies the ability of a filter to capture air contaminants/particles (including pollen) and a higher rating will help capture more. However, the air filters should be checked more frequently and replaced if needed due to the pollen accumulation.
Beyond the health implications, spring also gives way to changes in the energy demands of a building. Like the fall, the spring months have milder outside temperatures and humidity, lowering the energy demand required to maintain comfortable spaces. Rather than working against extreme heat losses (or gains) caused by the winter (or summer), your HVAC system may deal only with the heat gains caused by sources from the sun’s radiant heat, lights, and people. These heat gains still require cooling, but many times during the spring, the outside air conditions are cooler than the supply air from the HVAC system. Therefore, instead of wasting energy to mechanically cool air, an economizer can be used to condition your space. An economizer will allow your system to supply outside air directly to your building, thereby reducing or eliminating the need to use energy to cool your supply air. This is typically referred to as “free cooling” and can greatly reduce your energy consumption and costs.
In addition to being more cost-effective, economizers are inherently meant to bring in more outside air to your building and will help increase the indoor air quality – just remember those air filters! Although this equipment can provide significant cost savings after it is installed, it can be more complicated to integrate into an existing building design. Using the economizer strategy must be carefully thought out and designed to make sure that the system is running properly and efficiently.
You may not know where to start with improving indoor air quality or decreasing the energy consumption of your commercial space. Many factors and variables can affect the health of your occupants or the number on your bill — with an untrained eye, you might be unaware of your building’s limitations and energy saving potentials. In that case, it is a good idea to schedule a building energy audit and systems assessment with a professional mechanical engineering firm.
Experts will help you determine where your energy is wasted and how to decrease the waste. A professional understanding of your energy expenses and mechanical design will help you invest in the right solutions, protecting your occupants and saving you money in the long run.