Blog
View All Blog Postings
Melt Down
This is an interesting report from North Carolina about vinyl siding being melted by the reflection from energy-efficient windows. http://www.wcnc.com/home/Double-pane-windows-can-magnify-sunlight-and-melt-more-than-vinyl-siding-138679724.html
Corrosion Protection Plan
An effective corrosion protection plan is an essential aspect of the design, repair or maintenance of reinforced concrete structures such as parking garages and balconies or steel building frames wrapped in masonry, which are exposed to the elements. Severe corrosion of the embedded steel must be avoided so that the structure maintains its full strength.
Corrosion of steel embedded in concrete or masonry is an electrochemical process that occurs in the presence of moisture and oxygen, which can accelerate if the structure is exposed to deicing salts or a salt-water environment. Once started, corrosion will continue until it is controlled.
To control corrosion, the steel can be coated with a protective material such as zinc, paint, or epoxy. Alternately, the electrochemical process can be mitigated with cathodic protection. Coatings generally only protect the steel until the barrier is breached, while cathodic protection provides a more active means to address corrosion.
In cathodic protection, zinc anodes may be attached directly to the steel to alter the electrochemistry and force the steel to become the cathode and be protected while the zinc anode “sacrifices” itself. Anodes can be used in new construction as well as in the repair of existing structures.
Another form of cathodic protection, applies a small electrical current directly to the steel, which prevents the electrical process of corrosion from occurring. This system requires a power supply, a sacrificial anode, and instrumentation for monitoring.
Selection of the appropriate level of corrosion protection for an existing structure is based on many factors. Among them are the level of corrosion damage, environment around the structure, potential for corrosion activity, the cost and design life of the corrosion protection system, and the expected service life of the structure.
Avoiding Contract Liability
Anytime that a property retains a contractor to perform repairs or maintenance, the parties involved (typically the Building Owner and the Contractor) have certain responsibilities. Under most contracts, like those of the American Institute of Architects (AIA), it is required that the Contractor be solely and totally responsible for:
Supervision of the work and the activities of all employees;
The specific “means and methods” that are used to complete the work;
Safety of all work areas as well as the public that may pass through or near work being performed.
It is vitally important that the Building Owner not interfere with the work of the contractor in these areas or specifically direct the Contractor how to perform his work in regards to these matters. It is reasonable to discuss issues with the Contractor, review contract requirements, etc. However, if the Building Owner specifically directs the Contractor to perform work a certain way, the Building Owner may become directly responsible for any undesired consequences.
As always, check with your legal counsel regarding this issue and be careful about what you tell a contractor to do.
SEEKING ANSWERS!
Concrete can degrade and fail due many causes and sometimes the reason is not quite evident. We often use sounding techniques such as tapping with a hammer or chain dragging as well as chemical analysis or electrical measurements to diagnose concrete problems. When these simple tests prove inconclusive, we can send a concrete sample from the structure to a laboratory for petrographic analysis.
Concrete petrography is an effective technique for investigating the quality, workmanship, durability and defects of concrete. It involves the examination of the concrete with an electron microscope that can magnify the sample by up to 10,000,00 times and allows for the description of hardened concrete in the lab, using specialized techniques borrowed from those used in the study of rocks.
The analysis can provide a wide array of information that cannot be determined in the field such as:
- Information on the composition and construction of the concrete sample,
- Identification of the aggregates, the quality of the cement paste, and the bond between them,
- Determination of the water to cement ratio, which is a major factor in concrete strength,
-
Assessment of the concrete’s resistance to damage by freeze and thaw cycles, sulfate attack, alkali-aggregate reactions, aggregate durability, and carbonation, and,
-
Evaluation as to whether a failure was caused by a faulty mix design or poor workmanship during placement and curing.
We do not use this service too often, but when we need to know more about the concrete, petrography often gives us the answers that we are seeking.
Setting the Mood With Color
Color affects our perceptions of our surroundings, particularly indoor environments. As designers, we can use color to set the mood for a particular space.
For example, the use of warm colors like red, yellow, and orange can bring about feelings of excitement, motion, and imagination. This is particularly beneficial in spaces for children, entertainment, and retail sales.
Warm neutral colors like beige and brown evoke feelings of comfort and security. This is useful in commercial office or residential settings.
Cool colors like green and blue are calming, soothing, and inspirational. They promote feelings of freshness and growth and are suitable in medical and religious facilities, classrooms, etc.
Cool neutral colors like grey, charcoal, or stone are sophisticated and subdued. These colors lend themselves to commercial and industrial spaces.
Color is just as important as form in architecture, as it sets the mood.
Important (Behind the Scene) Components
While there is no one “most” important component of any given building envelope system, flashings are certainly critical parts. Whether it be roofing (flat or sloped), exterior cladding (brick, siding, EIFS, etc.) or windows and doors, flashings play a key role in the success of these systems.
Flashings can consist of metal, sheet materials, or even liquid-applied membranes and are typically located at key areas (window/door perimeters, wall transitions, penetrations through roofs or walls, etc.) that would otherwise be prone to leakage. Their primary functions are to keep water away from vulnerable components and/or redirect it away from interior spaces.
The cost of installing proper flashings is a relatively low percentage of an overall system. On the other hand, the effects and costs associated with missing or improper flashings can be extreme.
We regularly encounter the consequences when flashings are not included or are improperly installed. In addition to obvious problems (interior water penetration) rot or corrosion of framing and other concealed building elements can develop and progress unnoticed. Such damage can be extensive and even disturbing.
The accompanying photographs show what can happen when an EIFS assembly lacks flashings to collect and divert water away from internal elements. Repeated and prolonged wetting of the underlying wood components produced the severe damage you see and it went undetected until we opened the system up for inspection.
Difficult Flooring Problems…We Can HELP!
Buckled wood flooring, moldy carpets, peeling sheet flooring, and bubbles in liquid applied floors can all be signs of excessive or trapped moisture below the floor covering. Moisture permeating from concrete floor slabs affects the performance of flooring systems such as resilient and textile floor coverings and coatings, and can cause floor covering system failures such as, debonding and deterioration of finish flooring and coatings, as well as microbial growth. Manufacturers of such floor covering systems generally require moisture testing to be performed before installation on concrete. Omitting these tests when they are required by the Manufacturer may void the flooring system warranty. This is a relevant issue for new construction or any project where the flooring/coating manufacturer requires ASTM testing prior to the flooring installation.
All of the concrete slab moisture tests require proper surface preparation (removal of adhesives, previous coatings, surface impurities, etc.), followed by a waiting period (usually 72 hours) under typical ambient conditions. Three tests are required for the first 1,000 square feet of floor space, and one additional test is required for each additional 1,000 square feet. When the test results are compared to the flooring manufacturer’s installation requirements, they can indicate if the concrete slab is acceptable for the installation of resilient flooring.
Four different tests can be run on concrete slabs to check the moisture content. The ASTM F710 standard test method involves the measurement of the pH level of the concrete surface, which is required data for all three of the slab moisture testing methods. As Portland cement hydrates, calcium hydroxide and other alkaline hydroxides are formed. The pH of wet concrete is extremely alkaline, while the pH of a floor with at least a thin layer of carbonation is typically between 8 and 10.
ASTM F1869 measures the Moisture Vapor Emission Rate (MVER) of a concrete slab expressed in lbs/1000 ft2/24 hours. This is achieved by placing a dish of calcium chloride on the slab surface under a plastic cover, allowing the crystals to absorb moisture emitted from the slab over a 72 hour period, and weighing the dish after. Typically, flooring manufacturers require an MVER of 3 lbs/1000 ft2/24 hours or less before installation.
ASTM F2170 measures the relative humidity throughout the depth of the concrete slab as a percentage by drilling a small diameter hole into the slab. ASTM F2420 is another test that also measures the relative humidity of the slab as a percentage, but this uses an insulated hood positioned over a portion of the concrete slab. This method simulates the placement of resilient flooring on the concrete surface itself, but it is not commonly used in the United States.
So how long does it take for a concrete slab to dry out, and how soon should the slab moisture tests be performed? Unfortunately, the drying time for concrete slabs can vary greatly depending on atmospheric conditions and the mix design. However, a typical 4” thick slab with a water-cement ratio of 0.45 can take anywhere from 90 to 120 days to achieve an acceptable range. Slabs that contain lightweight aggregate or that only dry from one side (such as slabs installed over a moisture vapor retarder or on metal decking) may need a much longer drying time.
If the concrete slab does not meet the flooring manufacturer’s requirements for installation, it is advisable to wait at least 30 days before performing another set of tests. In the interim, you can perform a plastic sheet test per ASTM D4263 (commonly called a mat test), and if the slab appears dry, then a re-test using the more rigorous ASTM procedures, above, can be performed.
Please give us a call if you are experiencing flooring problems. We have a certified technician ready to help!!
And The Award Goes To….
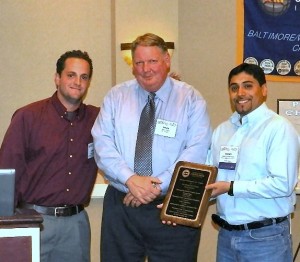
Bobby Radcliff of ETC, along with Mark Avon (Avon Corporation) take home 2nd place in the ICRI Outstanding Repair Project Award. This foundation underpinning project presented unique challenges and a very difficult engineering design. ETC was hired to address several major cracks in the foundation and differential settlement that had compromised the structural integrity of the building. A repair scheme and specification were designed based on soil boring at several site locations. One of the many challenges Bobby & Mark faced on this project were working INSIDE peoples homes over an extended period of time. Communication and scheduling played a huge part in making this project such a success.
ETC would like to give honorable mention to ALL the Homeowners and Management Staff at Huntington Club Condominium. Your patience and understanding were KEY in making this an AWARD WINNING PROJECT. We accept this award on your behalf!
Gotta Stay Flexible!
Large buildings and parking garages have expansion joints included in their original design to accommodate natural thermal movement (expansion and contraction), as well as to separate portions of the buildings with varying masses, so that expected swaying, such as with the wind, will not result in damage to the structure.
These joints effectively divide the structure/building into separate, smaller pieces and often must be sealed to prevent rain from entering the building. The joints cannot be filled with a solid, rigid material, so a flexible filler must be used that can stretch as far as is needed while remaining watertight.
Expansion joint filling materials typically have a service life of about 5-10 years. Selecting the proper joint filler is necessary to obtain suitable performance. Some considerations are:
1.) What type of traffic will it be subjected to? Pedestrian, automobile, heavy trucks, buses, snow plows,etc. 2.) Will the joint need a protective cover? 3.) Does the joint need to be watertight or fire-rated? 4.) How will the joint filler be incorporated into the adjacent waterproofing system? 5.) How much elongation and compression movement is expected? 6.)What Is the geometry of the joint itself and are there any turns or changes in direction?
Leaking or failed joints can result in damage to the structure, so the right material must be used to allow the structures to move independently, while remaining intact. Sometimes a simple caulk joint may be the proper choice, but more elaborate pre-formed materials are also available.
Sunny Thoughts…
Many of our clients have been considering the addition of solar panels to roofs to either generate electricity or make hot water. Several things to consider before adding a solar panel system to your building are:
1. Can the roof support the extra weight of the solar panels as well as resist the associated additional wind forces? Some solar arrays are ballasted (weighted down) and rest on the roof, which can be quite heavy and overload the roof.
2. Will the solar panel attachments penetrate the roof membrane/material and be properly sealed to prevent leaks?
3. How difficult will it be to replace the roof membrane after the panels are installed? What will be the cost of disassembly and moving the panels, when the roof needs to be replaced or patched?
4. What maintenance or cleaning is required of the panels and is there adequate access to allow for the required maintenance?
5. Will the building safely support the hot water tank required? These can have a large capacity and be very heavy.
Changes In The Wind
Changes in the wind have been felt lately; not only has the climate been influenced by this phenomenon, but design codes have been influenced as well. The American Society of Civil Engineers (ASCE) Standard 7 has released their latest 2010 issue, which is slowly being adopted by most local jurisdictions and it is likely that these changes will be included into the International Building Code (IBC) this year. The latest ASCE 7-10 code introduces new wind speed and windborne maps which change the determination of the basic wind speed, revised building classifications, and new methods for determining wind pressures for buildings.
So what does that mean to you and me? It means that higher wind pressures loading criteria for assuming safely, serviceabliity, and structural integrity are being implemented. In some cases the new wind loads can be 60% higher than previously required. This will affect the design and selection of stronger windows, doors, attachments for roofs, facades and mechanical equipment, and anything else that make up the building and its envelope.
Building Permits & Liability
When someone obtains a building permit to construct, alter or repair a structure, certain obligations become the responsibility of the permit holder. This includes the responsibility to complete the work covered by the permit properly, in compliance with the applicable code provisions, and in a safe manner.
If problems occur, the local code authorities look first at the name of the entity that obtained the permit. This would also apply to the individual who files a complaint with the local code authority regarding the work being performed.
Therefore, it is often in the best interest of the building owner that all permits be obtained by, and in the name of, the company actually doing the work at the property. This can provide a “first line of defense” against any potential work-related problems, especially any “nuisance” claims.
If permits are issued in the name of the contractor, building owners should require verification that the permit is properly “closed-out” with the issuing code authority when the work is completed. The satisfaction of this requirement can be a condition of final payment to the contractor for the work preformed
Consult with your attorney for legal advice regarding this matter and understand that requiring the contractor to obtain needed permits may not relieve the building owner of all legal obligations related to the work being performed.