Blog
View All Blog Postings
Superior Sealants!
Modern sealants (caulks) are vastly superior to those available in years past. They exhibit better flexibility and do so for longer periods of time. As good as the newer products are, they still must be properly applied if they’re to perform as intended.
As a general rule, sealant joints should be about half as deep as they are wide. Shallower than that, there’s not enough material to accommodate thermal contraction of the substrates (which widens the joint) without tearing. Deeper than that, the material can be distorted and/or pushed out of the joint when the substrates expand and narrow the joint. Elastomeric sealants also cannot accommodate full movement in two planes and three-point bonding can result in damage and reduced protection. Backer materials (to control joint depth) and bond breakers (to prevent three-point bonding) are critical elements of sealant joints.
Joint preparation is equally important. The joint substrates must be free of contaminants and in some cases, primed. A properly adhered joint will tear (fail cohesively) before it debonds. The accepted test for adhesion is to cut a cured joint across its width and a few inches along the substrates, then pull the freed segment at a 90 degree angle until it tears or pulls free from the substrates. If it pulls free before it tears, adhesion is inadequate.
Other important factors include temperature at the time of application and other weather considerations. Manufacturers will have requirements specific to their products and those must be complied with to assure performance and longevity.
The conditions necessary for sealant performance cannot be attained when applying new sealant over old. “Overshooting” caulk will produce results that are at best, temporarily or partly effective.
Putting Our Heads Together!
Locating the TRUE source of water intrusion can often be quite a challenge. A group effort is always the best approach. Without the knowledge of on-site building engineers and dedicated property managers, our job would be much more difficult. Wei Fung, Jose and David of Moore & Associates manage their properties with great care. We are pleased to be part of their valuable team!!
Chlorine Does NOT Play Nice with Others.
Remember to never store other chemicals (cleaning products, solvents, fertilizers, deicing agents, etc) in pool filter or pump rooms. The most widely used pool chemical is chlorine and it does not play well with others (particularly ammonia compounds). Very bad things can happen if they should mix, including creation of chlorine gas and other highly toxic substances. Ammonia is present in most fertilizers and a number of chemical deicers. Stay safe this summer and separate your chemicals!
Don’t Stay Out Too Late.
Commercial Waterproofing has performed concrete and masonry restoration projects with ETC for many years, so it was nice getting to visiting with some of their guys at the monthly ICRI meeting. Please allow me to introduce Jim Ninteman & Erick Mercado from Commercial Waterproofing and Lucas Salo & Nick Henn from ETC. Enjoy your evening fellows….it’s back to work early tomorrow morning!!
The Cost of Waiting
If you’re about to undertake a paving project that was deferred from last year, you can expect a cost increase due to rising crude oil prices. The liquid asphalt used as a binder in pavement is a petroleum product (a byproduct of gasoline production). Most paving contractors have escalation clauses in their proposals in anticipation of changes in oil prices and they’re usually based on a recognized industry index. Local indices are published by the Maryland Asphalt Association (www.mdasphalt.org ) and the Virginia Department of Transportation (www.virginiadot.org/business/const/indices-asphalt.asp).
Adjustments would be made according to a formula that factors in the differences between liquid asphalt costs (normally “short-ton” figures) at the time of proposal submission and acceptance. That difference would then be multiplied by some factor (typically .003 to .005) for an adjusted square yard increase, per-inch of thickness. As an example, a simple two-inch overlayment (without patching) at a 5,000 square yard parking lot that would have cost $100,000.00 ($20.00 per square yard) based on a liquid asphalt price of $465.50 would be increased by $6,520.00 based on the May 2011 asphalt price of $628.50 [(628.50-465.50=163) (163 x .004=.652) (.652 x 2=1.304) (1.304 x 5,000 = 6,520)]. Other increases for fuel and other operating expenses could also be incorporated into escalation clauses.
Crack Monitors
Cracks in brick walls are common. Figuring out whether or not they are serious and why they are happening can be challenging. Crack monitors can be installed to help document which way the wall is moving and how fast. We recommend that the monitors be left in place for at least a year, or until the movement becomes alarming. It is important to know if the wall movement is attributable to natural seasonal temperature changes or possible foundation settlement. Knowing why the wall is moving lets us determine what the proper repair should be. Sometimes a simple caulk joint can be the right fix, or a more expensive foundation underpinning project make be required.
No Stacking The Deck
Synthetic wood manufacturers have requirements on the size of the gaps required between their decking boards. We have seen some decks where the synthetic lumber was spaced so tightly that water ponded and ice was formed on the deck surface. Manufacturers offer very long warranties (up to 25-year) but they will not honor the warranty if the gaps are too small and a future problem can be attributed to improper spacing of the boards. Check with the manufacturer before you start to install synthetic decking for the side to side as well as end gaps that are required.
Shout Out!!
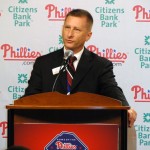
Just wanted to thank the many people involved with the CAI Pennsylvania Delaware Valley “Love Where You Live” Expo. This group of property management professionals must also “Love What They D0” because it sure showed in their efforts last week. Thanks to the staff of CAI: Tony Campisi, Executive Director; Mike Shaw, Marketing and Leanne Casner, Support Staff. Your fun venue and great educational classes made it a show that will just continue to grow . Also, a big thanks to Nancy Hastings of Mamco Property Management and the entire Expo committee for their time and dedication.
Anyone interested in finding out more about the Pennsylvania Delaware Valley Chapter of CAI, please visit their website at www.cai-padelval.org. They would be happy to answer any questions you may have.
Phantics for Philly
They don’t call this place the City of Brotherly Love for nothing! What a warm welcome we received at the CAI Philadelphia Expo. It was a pleasure meeting many new managers while enjoying the company of the legendary Phillie Phantic! Kudos to the CAI staff for a great event! I encourage anyone in the area to come and enjoy a day of gathering resources, meeting great people and indulging on a philly cheese steak or two. You won’t be disappointed. Hope to see you there next year.
Adding Parking Spaces
Expanding a parking lot by converting a landscaped area into parking space sounds easy, but in actuality the process can be quite complicated. As coveted as parking places can be, green space is not something you can necessarily sacrifice without a care. In many cases landscaped, wooded areas are protected by government ordinance or regulation. It’s by no means impossible in every instance to get a variance & permit, but don’t expect an easy time of it.
Even if you manage to avoid or get through the bureaucratic red tape, there’s a good chance that someone in the community will object to the loss of a tree or lawn. It’s not unheard of for such objections to degenerate into lawsuits.
After you’ve cleared the legal hurdles, you can expect to pay construction cost of $2,000 – $4,000, per space (depending upon factors too complex & numerous to discuss here). Engineering and permitting fees, feasibility studies, environmental impact studies, surface drainage calculations, etc. that may be needed before construction can begin could add considerably to the cost.
Whatcha Think?
Aggregates are added to concrete for what reason?
1) Inexpensive filler 2) Improved workablility 3) Dimensional stability 4) Increased wear resistance 5) All of the Above
All of the above is the correct choice. Basic concrete consists of the paste (Portland cement & water), fine aggregate (sand) and coarse aggregate (crused stone or gravel). Aggregates can account for up to 75% of the volume of concrete and are considerably less expensive than the Portland cement. They also play a substantial role in determining workability, strength, dimensional stability, and durablity of the concrete.