Blog
View All Blog Postings
Adding A Rooftop Deck
With Summer just around the corner, you may want to consider converting that unused roof area into a gathering spot with a beautiful view. Rooftop decks can be quite appealing, but before sending out the party invitations, make sure to consider these few helpful tips
- Hire a professional to specify maximum allowable occupants. Decks are designed for specific live loads (such as people, type of activity, snow, furniture) and specific dead loads (such as decking, pergola, railing). Therefore, design your deck for a specific number of people and specific activity.
- Ask your design professional about cross-bracing (lateral support), a very important building code requirement that affects the overall look of the deck.
- Study and understand exit requirements for your rooftop deck as specified in the building codes. Requirements for a multifamily residential building are more stringent and costlier than a single family home.
- Specify proper slope for water drainage. Our recommendation is ¼” per foot, although every situation should be carefully considered. Waterproofing of your deck and roof are very important factors of your project, if not properly built or maintained, it can cause problems and expenses for the residential unit below.
- Choose materials and construction details to last a long time. All framing should be pressure treated lumber and elevated above roofing material. Decking and railing material can be pressure treated or composite. Composite material is a mixture of sawdust, wood chips and vinyl. To keep it environmentally friendly, make sure the vinyl component is made from recycled plastic materials. Composite material is very low maintenance and there is no need for painting or staining.
- Pay special attention to lighting and controls, especially in areas such as stairs, change of levels and door entry/exit.
Scaling Concrete Surfaces
Is your concrete peeling or flaking in localized areas? Are you noticing rough, aggregate surfaces in your concrete that haven’t been there before, particularly after the latest round of winter weather? If so, your concrete may be experiencing a condition called scaling.
Scaling occurs when a thin layer of the concrete surface flakes, or scales, from the concrete element. Removal of this thin layer often exposes the underlying, open-pore structure of the concrete, which poses a durability concern. The most common causes of scaling are listed below.
- Non- or Low-Air-Entrained Concrete – Air-entrained concrete contains small voids which accommodate volume changes when water (i.e. precipitation) in the concrete freezes and expands. If the concrete is not properly air entrained, the concrete surface may be overcome by expansive forces during freeze-thaw cycles, resulting in loss of material.
- Unsuitable Concrete Mix – Concrete mixes with low strength (less than 4,000 psi in exterior, exposed conditions) or those with high water-to-cement ratios are more susceptible to water intrusion and deterioration.
- Excessive/Improper Deicing Agents – These chemicals can attack surface layers of concrete. These chemicals can also create brines (which have lower freezing points than fresh water), and can increase the number of freeze-thaw cycles.
- Poor Finishing – Overworked concrete surfaces or those that receive additional water and or finished with bleed water can result in reduced entrained air content or weak, thin, cementitious paste deposits at surfaces.
Repairing scaled concrete surfaces can prove difficult. If a proper bond is not achieved between the cementitious topping/overlay and the underlying concrete, additional scaling or delamination may occur. If scaling is prevalent in your community, contact a professional engineer to determine the extent of the damage and to develop the proper repair strategy.
Hold the Vacuum! (Dusting Concrete Surfaces)
Have you noticed dry, powdery deposits on the concrete elements in your community? Or have you walked across concrete and had a white, dust-like powder follow you? If so, your concrete may be experiencing a condition called dusting.
Dusting occurs when the surface of concrete disintegrates, resulting in a loose, chalk-like powder. A list of potential causes of dusting is provided below.
- Poor Finishing – The addition of too much moisture during finishing operations, or condensation of cool air on the fresh, warm concrete surface can result in a weak surface layer. As pedestrian or foot traffic is applied to this soft surface, dusting may result.
- Poor Placement Conditions – Improper ventilation in an enclosed space where machines producing carbon dioxide are present, such as a garage, could result in carbonation of the concrete. This chemical reaction reduces the concrete strength, which may lead to chalking surfaces.
- Improper Curing – The omission of moist curing (i.e. wet burlap) operations or approved curing compounds can allow the surface of fresh concrete to dry out, resulting in a soft surface, susceptible to disintegration.
- Insufficient Protection – Newly placed concrete subjected to an unexpected summer rain storm, high winds, or freezing overnight temperatures without proper protection are prone to weakened surfaces and even reduced strength.
The good news is repairing this condition can be relatively routine. Sandblasting or pressure washing can remove the soft surface, or applying a hardener or sealer may also be effective. However, if the dusting/surface deterioration is severe, application of an overlay or topping may be necessary. If your community is experiencing dusting or you have concerns with your new concrete, consult with a professional engineer who can help evaluate and determine the appropriate repair solution.
Our Columbia Office Has Relocated!
Due to our growing need for space, we have relocated our Columbia office. Please note the address & phone number change…we would hate to miss your call!
Achieving The Sound of Silence
A common deterrent to personal enjoyment in multi-family buildings is sound transmission. Often determining what is too loud is subjective and measured by the sensitivity of our ears. The Building Code requires that walls and ceilings meet an STC (Sound Transmission Class) rating of 50 and an IIC (Impact Insulation Class) of 50. STC is related to airborne noise like a television, speech, or music and IIC correlates to footfalls or a dog’s toenails when they impact a tile floor.
At an STC rating of 50, loud talking cannot be heard but load music can be noticed. We usually are asked to investigate sound transmission concerns in wood framed buildings when the thuds of foot traffic of the resident or their pet, above, is perceived to be disturbingly excessive. Many condominiums have rules related to the percentage of the floor area that must be covered by carpet. This is likely because most carpeted floors comply with a IIC 50 sound rating.
Manufacturers of products used to construct wall and ceiling assemblies have their materials tested in a laboratory with various combinations of framing, drywall, and insulation to determine the STC rating. To inspect a noise concern, our first step is to review the available architectural drawings to determine the intended design and the associated STC rating for the wall and/or ceiling construction. Then we will cut a few holes at inconspicuous places to confirm if the drawings were followed. Most people are surprised to learn that no insulation was placed inside the wall or ceiling and that many assemblies can achieve the required STC rating without insulation.
Products are available that can be installed on floors, walls, and ceilings to reduce the offending sound transmission. Installing these materials can be limited to sleeping areas to save cost and the amount of disruption that the project has on a living space.
Satisfactory remediation of a sound problem can be difficult. Our ears will perceive a reduction in noise by one half when the STC rating is increased by about 10 points. Conversely, anything less than a10 point change is hard for people to distinguish. Finally, any expectation that a once noisy unit located within a multi-family building will become “sound proof” or like a recording studio after remedial work is complete is unrealistic
Fitness Center Facelift
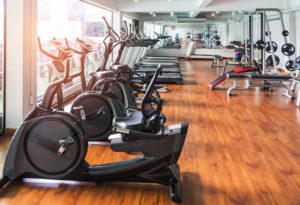
Here is our list of latest design considerations if you are planning to add a fitness center to your facility.
- Understand the type of desired physical activity that suites your community: for example, does your community want cardio equipment more than weights or do they require instructional studio-type facility.
- Understand local code requirements and have a professional perform code analysis and a feasibility study for your space/facility.
- The growing trend and appreciation is towards flexible space that can be tailored to any type of exercise activity such as stretching, yoga or pilates.
- End-users enjoy natural daylight during the work out; therefore, if the space allows, fitness center should be located near the window façade of the building.
- Entrance to the fitness center should be well marked with signage and preferably with glass doors and windows.
- Ceilings are a big area for cost savings. Often finish ceilings are not installed in the fitness center, painting the existing structure is all that is needed.
- LED light fixtures and simple ceiling fans are desirable and readily available at any hardware store.
- The growing market is towards less equipment and more open space. A gym equipment company which offers both buying and leasing options should be consulted. Make sure to incorporate WIFI and TV connectivity to the gym equipment.
- Walls of the fitness center should be painted with light and vibrant colors that reflect daylight into the room.
- Floor of the fitness center should be rubber mats strong enough to support heavy traffic and exercise equipment. Rubber floors are available in rolls and tiles with a variety of colors and textures.
- Add a self-service water coolers or cold drink vending machines area. Water fountains should be strategically placed and handicap accessible.
Do You Have The Engineer Disease?
Just a little humor to start the week.
Is Your Building Gasping For Air?
If you experienced one or all of the following situations inside your building, most likely your building (and you) need a little more fresh air.
1. Did you see condensation on your window pane in the winter? Without enough fresh air and proper ventilation to remove the moisture from inside the building, humidity will keep building up in the air. When the moisture content of air reaches the level of the dew point at the cold surface of the window or any cold spot inside the building, condensation will start to form and accumulate. When too much condensation is present, water may drip into the wall cavity and cause damage. In addition, high humidity will encourage growth of mold and mildew.
2. Do you always smell something “unique” in your house as soon as you step into the building from outside? Is it your favorite food smell, kitty litter smell or air freshener smell? This means you don’t have enough fresh air to push the old and stale air out of the building. Proper ventilation will get rid of this “unique” household odor and provide you and your visitors a fresh and clean air smell.
3. Ever wonder why you don’t quite feel energetic and frequently feel sleepy staying inside the building? Maybe some fresh air can help. Fresh air provides you with a steady supply of oxygen which is needed by your brain and every single cell of your body. Time to treat your body with a good supply of fresh air.
It doesn’t take a genius to figure out your building doesn’t have enough fresh air. However, it definitely takes a professional engineer to evaluate, analyze and design a cost effective and energy efficient ventilation system to provide adequate and comfortable fresh air supply year round
The Millennials
Millennials are defined as a generation of people whose age ranges from 18 to 34, that means born after 1981 or before 1999. This age group that has surpassed baby boomers in population are characteristically confident, self-expressive, multi-cultural, open to change and technically savvy. Millennials are not only aware of the latest market trends in design, they also expect their living environment to be up to the latest standards of design and construction. In conversation with recent Millennials buyers for condominiums, we discovered some of their priorities and expectations.
- Building preferably located from a walking distance to train station, grocery store, restaurants and school. There is a strong preference for centralized community living and vibrant neighborhood.
- Paper-less communication for all condominium announcements and meeting notes.
- Outdoor jogging/walking trail and a dog park should be located nearby, if not on the building premises.
- Automated control system for the condominium such as window shades, lighting and thermostat.
- A well-lit spacious lobby that welcomes not only the visitors, but also serves as a lounge area for the residents to meet and greet. Front desk should have also a package delivery service.
- Light fixtures should have motion detectors that could save their electrical bill and energy consumption.
- Bike repair station and bike lockers should be located near parking garage, along with electrical charge stations for hybrid cars.
Self-Healing Concrete
Researchers at the Delft University of Technology in the Netherlands are working on placing bacteria in concrete mixes to fix cracks in concrete and make it self-healing. This could make concrete less susceptible to damage related to water that infiltrates a beam by way of a crack and results in rebar corrosion.
http://www.citg.tudelft.nl/en/research/projects/self-healing-concrete/
Warranty Expiration Dates
What do you really know about your roof warranties? There may be separate warranties issued for various materials and the installing contractor may have also guaranteed workmanship. Each will expire at some point and there are things you should do to preserve your protections.
1. Review the documents and assure they were properly executed. If, for example the papers were never signed and returned to the manufacture, you probably don’t have a warranty.
2. Be aware of your responsibilities. Failure to properly maintain the system could void warranties.
3. Properly notify all involved parties (manufacturers, contractor, etc.) of problems within the 10 to 30 days typically required.
4. Be sure that repairs are made using approved materials and contractors certified by the manufacturer. Unapproved materials and repairs may void coverage, at least in the areas affected by repairs.
5. Have a knowledgeable person evaluate the roof covering periodically and within six months to one year in advance of warranty expiration dates. There may be conditions that could be corrected at no cost before coverage lapses.
Some warranties can be extended or renewed for additional cost; however it may not always be advantageous to do so. The manufacturer could impose maintenance or rehabilitative requirements that are unreasonable when compared with the value of the coverage. Spending $100,000 to get a five-year warranty extension on a $200,000 roof might not be the best use of the money.